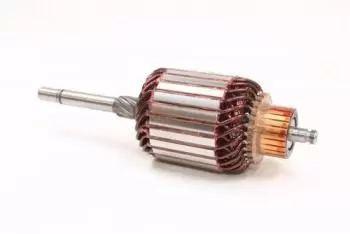
L'armature est un composant d'une machine électrique, chargé de convertir l'énergie électromagnétique en énergie mécanique (mouvement rotatif) par induction électromagnétique.
Cet élément est couplé magnétiquement à l'inducteur, qui est la partie de la machine où la force électromotrice (FEM) est générée par induction.
Dans les moteurs à courant continu (CC), l'armature est généralement située dans le rotor, tandis que dans les moteurs à courant alternatif (CA) asynchrones, l'armature peut être située dans le stator, également appelé moteur à induction. Cette conception est basée sur l'interaction entre les champs magnétiques générés par le stator (en AC) et le rotor (en DC).
L'armature électrique dans les moteurs à courant continu
Dans les moteurs à courant continu, l'armature est la partie rotative de la machine.
Il s'agit d'un tambour constitué de tôles de fer au silicium, d'une épaisseur d'environ 0,5 mm. Ces feuilles sont empilées les unes sur les autres et présentent des fentes à l'extérieur, où sont placés les enroulements du moteur. Lors de la rotation dans le champ magnétique généré par l'inducteur (situé dans le stator), une force électromotrice (FEM) est induite dans les bobines d'induit, générant du courant.
Les extrémités des bobines sont reliées à de fines feuilles de cuivre réparties sur la périphérie d'un cylindre isolant appelé collecteur. Le collecteur a pour fonction de relier les bobines d'induit au circuit électrique externe au moyen de balais de charbon qui frottent sur les dents. Ce système est responsable du fait que le courant dans les bobines est unidirectionnel, permettant au moteur de tourner en continu dans une seule direction.
Le commutateur, composé de barres, joue un rôle crucial car il permet l'inversion périodique du sens du courant dans les bobines, garantissant que le moteur continue de tourner. Bien que traditionnellement les moteurs à courant continu utilisaient ce système avec balais et commutateur, il existe aujourd'hui également des moteurs à courant continu sans balais (BLDC, Brushless DC), qui utilisent la commutation électronique pour contrôler le flux de courant sans avoir besoin de contact physique.
L'armature des moteurs à courant alternatif (moteurs à induction)
Dans les moteurs à courant alternatif, en particulier dans les moteurs à induction asynchrones, l'armature est également appelée rotor.
Ce rotor, situé dans la partie mobile du moteur, interagit avec le champ magnétique généré par le stator. Dans ces moteurs, le courant n'est pas fourni directement au rotor, mais y est induit en raison du champ magnétique variable créé par les courants dans le stator. Cette induction génère un champ magnétique dans le rotor qui interagit avec le champ magnétique du stator, produisant le mouvement rotatif.
Le rotor de ces moteurs est généralement de conception à cage d'écureuil, dans laquelle les conducteurs sont disposés de manière fermée à l'intérieur du rotor, sans connexion directe au circuit externe. Le courant induit dans ces conducteurs est ce qui provoque la rotation du rotor dans le champ magnétique du stator.
L'armature dans les alternateurs
Dans les alternateurs, qui sont des machines qui convertissent l'énergie mécanique en énergie électrique sous forme de courant alternatif, l'armature est située dans le rotor, tandis que le stator agit comme inducteur.
Dans ces générateurs, le rotor est composé d'un cylindre creux de tôles d'acier au silicium, disposées les unes sur les autres. Ce cylindre comporte des fentes à l'intérieur, où sont insérées les bobines.
Lorsque le rotor tourne dans le champ magnétique créé par le stator, une force électromotrice est induite dans les bobines du rotor, générant un courant alternatif.
À l'extérieur du boîtier de l'alternateur se trouvent les bornes qui permettent de connecter les bobines d'induit au circuit électrique externe, où le courant généré est délivré. Ces bornes permettent au courant alternatif induit de circuler dans le système électrique auquel il est destiné.
Matériaux et efficacité de l'armature
L'armature est constituée de matériaux conducteurs hautement efficaces, tels que le cuivre ou l'aluminium, en raison de leurs excellentes propriétés électriques.
De plus, des feuilles de fer au silicium sont utilisées pour former le noyau de l'armature, car elles aident à réduire les pertes par courants de Foucault (courants de Foucault) et les pertes par hystérésis en minimisant la résistance au passage du flux magnétique.
Ces pertes sont l'une des sources d'inefficacité des moteurs électriques. L'optimisation de la conception de l'armature, la réduction de l'entrefer et l'amélioration des matériaux sont donc essentielles pour augmenter les performances de la machine.
Autres types de moteurs électriques
Il existe d'autres types de moteurs dans lesquels l'armature joue un rôle crucial, tels que les moteurs synchrones et les moteurs pas à pas.
Dans les moteurs synchrones, le rotor tourne à la même vitesse que le champ magnétique du stator, ce qui les rend idéaux pour les applications nécessitant une vitesse constante. Dans les moteurs pas à pas, l'armature (rotor) se déplace par étapes discrètes, permettant un contrôle précis du mouvement.
Enroulement de l'armature
Les enroulements d'induit sont un élément crucial dans la conception des moteurs électriques, car ils sont responsables de la génération du courant électrique par interaction avec le champ magnétique.
Ces enroulements sont les conducteurs enroulés qui, lorsqu'ils sont soumis à un champ magnétique variable, induisent un courant qui génère la force électromotrice (FEM) nécessaire pour produire le mouvement dans les moteurs électriques.
Types d'enroulements dans l'armature
Les enroulements d'induit peuvent être conçus de différentes manières en fonction du type de moteur et de ses exigences de fonctionnement. Les principaux types d'enroulements utilisés dans les induits de moteurs électriques sont décrits ci-dessous :
Enroulement de fente
Il s’agit de la conception la plus courante dans les moteurs électriques. Dans ce type d'enroulement, les conducteurs (généralement en cuivre ou en aluminium) sont placés dans les fentes présentes dans le noyau de l'armature (ou du rotor dans certains cas).
Les fentes sont conçues pour loger les bobines de manière compacte, permettant une distribution efficace du champ magnétique.
Ce type d'enroulement peut être monocouche ou multicouche. Les enroulements multicouches sont utilisés dans les moteurs de plus grande puissance car ils permettent un plus grand nombre de tours de fil dans chaque fente, augmentant ainsi la capacité de courant du moteur.
Enroulement en spirale
Dans ce type d'enroulement, le conducteur est enroulé en continu en spirale le long de l'armature. Cette conception est la plus courante dans les moteurs de petite puissance ou les moteurs sans balais (tels que les moteurs BLDC). La disposition en spirale permet une meilleure gestion de l'induction et une meilleure répartition du courant.
Enroulement annulaire
Dans les moteurs à courant continu, en particulier dans les premières versions, les enroulements étaient généralement placés dans des anneaux entourant le noyau de l'induit.
Cette conception était moins efficace, car le courant induit devait traverser un espace plus grand en raison de l'entrefer, ce qui entraînait un champ magnétique plus faible. Cependant, cette conception a été remplacée par des fentes pour améliorer l'efficacité et réduire les pertes par friction.
Caractéristiques des enroulements d'induit
Les enroulements d'induit présentent un certain nombre de caractéristiques importantes qui affectent les performances d'un moteur électrique :
Nombre de tours de câble
Le nombre de tours dans l'enroulement a un impact direct sur la force électromotrice générée. Plus le nombre de tours est élevé, plus la force électromotrice induite est importante, ce qui augmente l'efficacité et la puissance du moteur. Cependant, plus de tours signifie également une plus grande résistance et donc une plus grande dissipation de chaleur. Il est essentiel de trouver un bon équilibre entre le nombre de tours et la résistance du bobinage.
Distribution des enroulements
La façon dont les conducteurs sont répartis dans les fentes de l'armature affecte la qualité du champ magnétique généré et l'efficacité du moteur. Les enroulements sont conçus pour répartir uniformément le courant dans l'armature, minimisant ainsi les pertes par courants de Foucault (pertes d'énergie dues aux champs magnétiques indésirables).
Type de matériau conducteur
Les matériaux utilisés pour les enroulements, généralement du cuivre ou de l'aluminium, doivent avoir une conductivité élevée pour maximiser l'efficacité du courant induit. Le cuivre est le matériau privilégié en raison de son excellente conductivité électrique, bien que l'aluminium soit utilisé dans les moteurs à moindre coût en raison de sa densité et de son coût inférieurs.
Isolement
Les enroulements d'induit doivent être isolés pour éviter les courts-circuits entre les bobines et le noyau d'induit. L'isolation doit également être résistante aux températures élevées générées par les courants électriques. Les matériaux couramment utilisés pour l’isolation comprennent les résines époxy, les peintures isolantes et le papier imprégné. De plus, l’isolation contribue à réduire les pertes par courants de Foucault.
Orientation de la fente
L’orientation des fentes dans l’armature affecte directement la qualité du champ magnétique induit. Les fentes peuvent être symétriques ou asymétriques. Dans les moteurs à haut rendement, la disposition des fentes est optimisée pour réduire les pertes harmoniques et améliorer la distribution du flux magnétique.